在航空航天領(lǐng)域,柔性電路板(FPC)因其輕薄、可彎折的特性,廣泛應(yīng)用于衛(wèi)星、飛行器的復雜空間系統(tǒng)中。但嚴苛的環(huán)境條件(如溫度、強輻射、劇烈振動)對 FPC 折彎工藝提出了可靠性要求。實現(xiàn)高可靠性的 FPC 折彎工藝,需從材料選擇、設(shè)備優(yōu)化、工藝控制及檢測驗證等多方面協(xié)同突破。 材料層面,航空航天 FPC 優(yōu)先采用聚酰亞胺(PI)等高性能基材,其具有 - 269℃至 400℃的寬溫適應(yīng)性與優(yōu)異的耐輻射性能。同時,需通過添加納米增強材料提升基材柔韌性與抗疲勞能力。導體材料則選用鍍金銅箔,利用金層抗氧化、抗腐蝕特性,保障電路長期穩(wěn)定導通。
設(shè)備上,定制化 FPC 折彎機需配備高精度伺服電機與閉環(huán)控制系統(tǒng),確保折彎角度誤差控制在 ±0.1° 以內(nèi)。引入激光測距與視覺檢測系統(tǒng),實時監(jiān)測折彎過程中的應(yīng)力分布,避免因局部應(yīng)力集中導致材料損傷。此外,設(shè)備需具備潔凈環(huán)境適配能力,防止顆粒污染影響 FPC 性能。
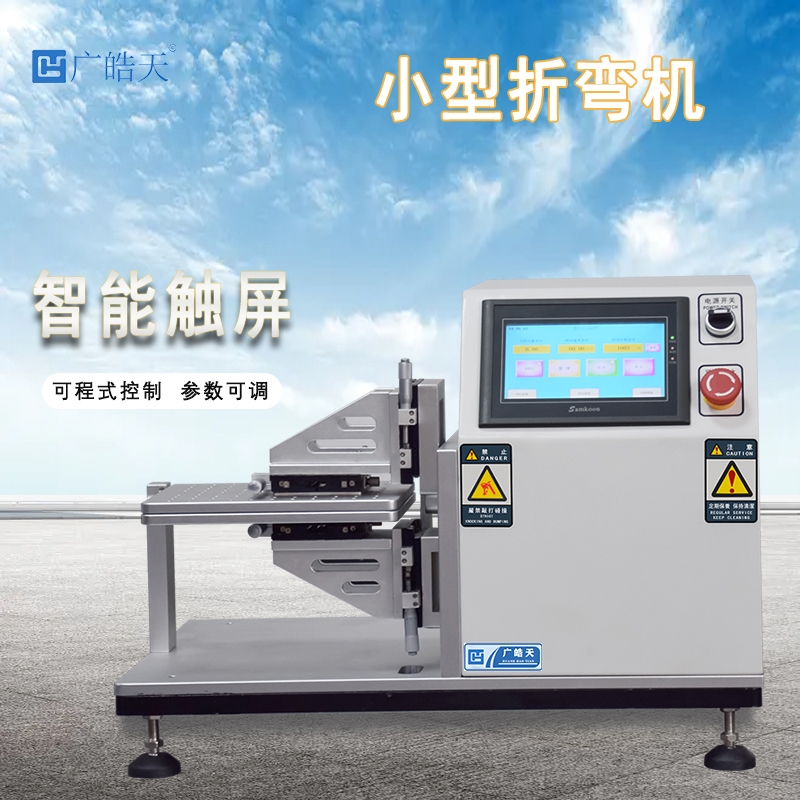
工藝控制方面,采用分步折彎策略,通過多次小角度彎折替代一次性成型,降低材料內(nèi)應(yīng)力。結(jié)合有限元分析(FEA)模擬折彎過程,優(yōu)化折彎半徑、速度等參數(shù),確保在滿足空間布局的同時,將 FPC 的疲勞壽命提升 30% 以上。生產(chǎn)過程中嚴格執(zhí)行 SPC(統(tǒng)計過程控制),對每批次 FPC 進行抽樣應(yīng)力測試,建立工藝參數(shù)與可靠性關(guān)聯(lián)模型。
檢測驗證環(huán)節(jié)是保障可靠性的最后關(guān)卡。采用 X 射線分層成像技術(shù)檢測 FPC 內(nèi)部層間結(jié)合狀態(tài),利用熱循環(huán)試驗(-55℃至 125℃,1000 次循環(huán))模擬環(huán)境。此外,通過振動臺測試驗證折彎處的機械穩(wěn)定性,確保 FPC 在復雜工況下仍能穩(wěn)定工作。
通過材料、設(shè)備、工藝與檢測的全流程優(yōu)化,航空航天領(lǐng)域 FPC 折彎工藝得以滿足嚴苛的可靠性標準,為精密電子系統(tǒng)的穩(wěn)定運行筑牢根基。